
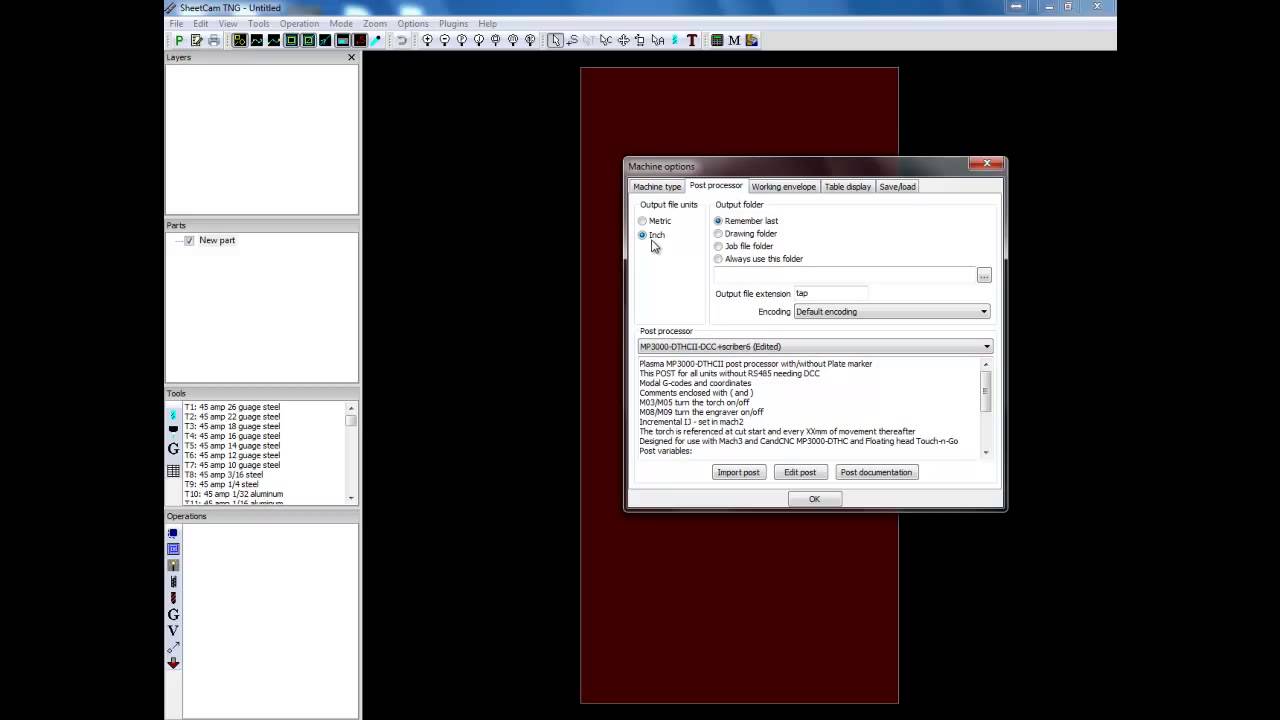
Which side to cut on is also defined with the click of a button. SheetCAM is designed so lead-ins and lead-outs are defined with a click of a button. one for computer one for CandCNC controller.talk to electrician about isolating circuits. Practical ound everything with the overkill mode even make it e uninterruptible power supplies on all electronics. The plasma table was 8'x10' used a CandCNC controller, wiring and steppers, and a Hyperthern plasma torch, run by MACH3, so all the electronics were hardwired together.touch height, xoyo, plus the cutting speed, height and all the other parameters that are needed for efficient plasma cutting. My perspective on this is from having owned a CNC plasma cutter as well as a 3-axis router, and having used CAMBAM, and SheetCAM. It is inexpensive as well, plus there are several add-ons that will helps speed production. Instead of trying to make CAMBAM function with a CNC plasma cutter, I strongly suggest that you use SheetCAM as it was designed from the ground up to be used with a plasma cutter. This "solution" may get me in trouble but here goes. It also show the behavior when optimization = none and changing the start point of the polyline itself (in this case the new start point of a polyline is always on a polyline point of course) The toolpath filter is used to show the order used to cut the shapes
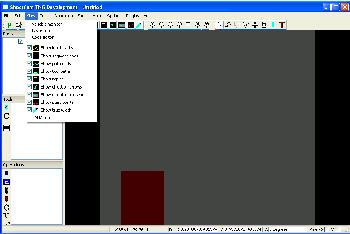
This other video show the behavior with 2 shapes in a MOP with optimization = 0.98 and optimization to none. the start point for each shape is the first point of the polyline The first machined object is the first in the ID list of the MOP


If the optimization property is set to none, the rules change and start point is ignored. So, I think that for plasma cutting, the best way is to use one MOP per shape so you can set the start point for each shape as you want. Note that if more than one shape is used in a MOP, only the start point for the first shape can be set the start point (and the cut order) for other shapes is the closest position from the end of the toolpath of the previous one. This video show start point on a polyline (closed) and on a circle. For me, changing the start point works well, and it's not needed to insert extra point in a polyline.
